You may have heard or read about improving your soil health or soil quality over the last year as this area of field management gains more attention. But what exactly do the terms mean and how can you incorporate the concepts in your day-to-day soil management practices? In Part 1 of this article series, the physical and chemical connection to optimizing soil quality by focusing on the structure of your soil will be explored.
Soil Quality and Health
Soil quality has broad application to your farm. It refers to how well a soil functions physically, chemically and biologically and how well it does its “job” (Fig. 1, page 6). For example, a forest soil has a different job than a farm soil, and soil properties can be measured on how well the soil is performing (e.g. soil structure).
Many factors influence the soil quality on a farm and are summed up in Figure 2, on page 7. In this article, the focus will be on the physical and chemical management practices that maximize soil quality, expressed here as soil structure (Fig. 3).
Soil health refers to the interaction between organisms and their environment in a soil ecosystem concept and the properties provided by such interactions (e.g. ecosystem stability). When you think of soil health, think of the biological integrity of your field (e.g. microbial population and diversity) and a focus on supporting plant growth. This will be the focus of Part 2 of this article series.
Poor soil structure and the resulting decrease in soil quality continues to impact yields in many farming areas. This is because many factors can negatively impact soil structure, including soil compaction from field equipment, poor salinity management, rainfall and irrigation droplets, excessive tillage, etc. Fortunately, fields that have poor structure (see Fig. 3 for a visual reference) can be fixed once you determine what is causing the issue. I strongly recommend that you put your field detective hat on and work with your favorite Certified Crop Adviser (CCA) to diagnose why your field is not performing as expected.
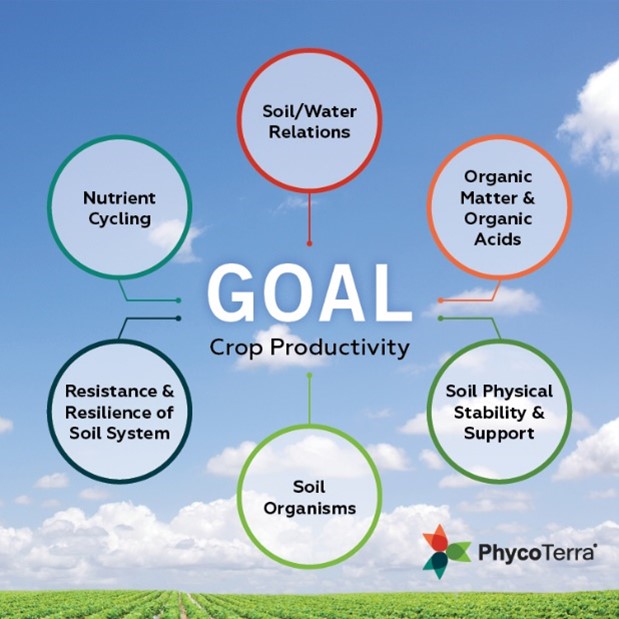
Physical Controls
Physical and chemical management strategies are important to help reverse poor soil structure and thus improve the overall soil quality of your field.
The physical controls on soil structure generally relate to reducing disturbance to the soil and protecting the soil from future disturbance. With this broad mandate, there are a variety of techniques out there to accomplish this goal and help restore soil structure, but reducing tillage and incorporating cover crops into the growing operation are the most important.
Tillage Practices and Soil Structure
Field activities like tillage are crucial for any successful growing season, whether in the short term or long term. However, excessive tillage can be hard on your soil structure as common implements can slice, compact or crush soil aggregates and quickly change a soil from having excellent tilth (see right side of Fig. 3) to one that lacks those properties (see left side of Fig. 3). The physical destruction of aggregates can have an immediate impact on your soil quality and can impact your operation’s bottom line. Fortunately, there are many modern options for avoiding excessive tillage, including conservation tillage and residue management, strip tillage and even a complete elimination of the practice (no-till). Every operation is different, and changes in tillage need to take local growing practices into account before moving forward. Reducing tillage has been shown to improve soil structure and soil quality; however, pulling it off can be tricky. It is worth noting that some tillage can be beneficial (e.g. deep ripping of hard pans) but should be employed only when necessary to help avoid impacts on soil structure.
Cover Crops
This concept is related to keeping the soil covered and physically protected from disturbance into the future after the crop is planted. The cover crop, usually grown in between the rows of permanent crops (e.g. trees and vines) or in the ‘off-season’ for annual crops, can be used to shield the soil from wind and water erosion and also help open up soils that have a history of poor soil structure. Briefly, the canopy of a cover crop can intercept and slow the velocity of raindrops and break up wind gusts, which helps keep soil on the field.
Belowground, the root systems of cover crops can poke through clods and hard pans and help open up channels in the soil profile to help move water downward into the profile. Fine root hairs can also tie soil particles together, improving soil structure and quality.
Please contact your preferred CCA for more advice on tillage practices and cover crop selection and to see if it fits into your farming operation.
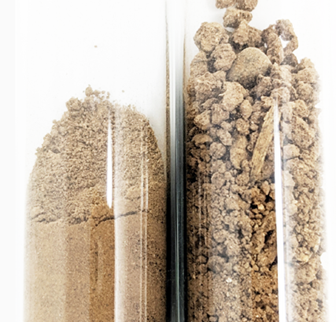
optimized crop growth (photo courtesy K. Wyant.)
Chemical Controls
A common issue in fields that have poor soil structure and soil quality is related to a chemical relationship in the soil. A loss of soil structure due to a mismatch between soil structure, calcium and other elements is called deflocculation. Under normal conditions, soil particles with ample calcium naturally come together to form aggregates, which improves soil structure. When the calcium is displaced by other ions (e.g. sodium), the soil structure collapses, and soil quality can quickly deteriorate. One of the main goals of a chemical remediation program is to provide more calcium to the soil, thus reversing the collapse in soil structure and driving an improvement in soil quality. The question is, “Which calcium amendment do I use?”
I cannot stress enough the need to start your program with a soil sample and to utilize the experienced advice from a CCA. Taking a soil sample will help you figure out the following important parameters critical to your chemical program: 1) Which amendment to use (e.g. gypsum, lime, sulfur product); and 2) Dosage of correct amendment to apply.
Critical parameters on the soil report worth looking at are soil pH, fizz test results, EC (dS/m), SAR, sodium and chloride results. For example, the fizz test measures the amount of free lime in a soil (CaCO3), and this is either expressed qualitatively (low, high, etc.) or quantitatively (%). There are a few major bulk calcium amendments that are available to help restore your soil structure: lime, gypsum and sulfur products.
Lime
Lime (CaCO3) is commonly used in soils that are acidic with soil structural issues and should not be confused with ‘free lime’ that shows up on a soil test report. Lime can provide a calcium source while also neutralizing acidic soil pH. Thus, soil quality can be improved on two separate fronts (soil structure and soil pH) with one program. Calculating the liming rate for a field (lbs/acre) can be tricky since you have to factor in both the amount of calcium needed to fix your soil structure problem and the amount needed to adjust the pH. A good soil sample and an experienced CCA can help determine the optimum rate for your field.
Gypsum
Gypsum (CaSO4) is a calcium amendment when one has low or very low fizz test readings. This is one reason why I recommend that you start your program with a soil test. When gypsum dissolves, it can supply calcium directly to the soil, which improves soil structure and allows excess salts (e.g. sodium) to drain. However, unlike lime and sulfur products, gypsum will have little impact on soil pH and should only be used to provide calcium to help restore soil structure and soil quality. An experienced CCA can help interpret your soil test and provide a reasonable gypsum recommendation (lbs/acre) to fix the issue.
Sulfur Products
Sulfur products, such as sulfuric acid and elemental sulfur, require the presence of free lime in the soil (CaCO3). As such, soils that have medium to very high fizz test ratings are a great candidate for the use of sulfur products in your chemical reclamation program. Briefly, sulfur products react with the free lime in the soil to create gypsum as a by-product. The calcium in the gypsum is then able to go to work to improve soil structure. One advantage of using sulfur products is that you generally do not need as much material to get the job done as you do with gypsum (1 ton gypsum = 0.57 tons sulfuric acid = 0.19 tons elemental sulfur), which can impact field logistics and application costs.
Also, repeated applications of sulfur products can reduce problematic soil pH areas by moving the soil pH from alkaline to neutral. One disadvantage to using sulfur products is that they have several reaction steps that can slow the reclamation speed of the field relative to lime and gypsum. Also, sulfuric acid products present some safety concerns that must be considered from a worker safety and transport level. Like lime and gypsum, an experienced CCA can help interpret your soil test and provide a reasonable recommendation (lbs/acre) to fix the issue.
Conclusion
Physical and chemical factors can have a profound impact on your overall soil structure and, thus, the soil quality of your field. Generally, poorly structured soils have a difficult time supporting optimized crop growth due to the severe reduction in water storage capacity, low oxygen, surface crusting and seed bed issues, accumulation of salinity, etc. If your soil looks like the example on the left side of Figure 3, it may be well worth your time and money to start implementing soil improvement practices as outlined in this article. You have a variety of management options, including the implementation of practices that improve the physical components of soil quality (e.g. tillage reduction and use of cover crops) or the chemical components such as adding bulk calcium amendments to your program. A bit of detective work beforehand determining why your field is having a soil structure problem can pay off in turning your field around and using your input dollars most effectively.
In Part 2 of this article series, we explore the biological components that influence soil structure and soil health. We will define soil health and go through plenty of examples on how the living component of a soil can impact your soil structure and overall soil quality. Furthermore, we will discuss how to test for soil health in the field.
Suggested Reading
- Soil Health Partnership Blog – https://www.soilhealthpartnership.org/shp-blog/
- Soil Health Institute Blog – https://soilhealthinstitute.org/resources/
- PhycoTerra® Blog – phycoterra.com/blog/
Dr. Karl Wyant currently serves as the Vice President of Ag Science at Heliae© Agriculture where he oversees the internal and external PhycoTerra® trials, assists with building regenerative agriculture implementation and oversees agronomy training. Prior to Heliae Agriculture, Dr. Wyant worked as a field agronomist for a major ag retailer serving the California and Arizona growing regions. To learn more about the future of soil health and regenerative agriculture, you can follow his webinar and blog series at PhycoTerra.com.