Many of the pesticide application technologies used in specialty crop production today are based on axial fan air-blast sprayers (Figure 1). Air-blast sprayers were first developed in the 1950s when orchard trees were 20 feet tall or more; today orchard trees of many crops are 7 to 13 feet tall. Air-blast sprayers are versatile and reliable and can be modified to fit numerous types of crops. Despite their popularity, standard axial fan air-blast sprayers have long had a reputation for inefficient application characteristics. For example, spray landing on the ground from radial air-blast sprayers can be from 20% to 40% of total applied spray volume. To improve application efficiency, sensor-controlled spray systems were designed in the 1980s as a way to reduce labor costs and pesticide waste. Sensor-controlled spray systems are receiving renewed interest as their reliability has improved and more options have become available.
Sensor Sprayer Types
There are two main types of sensor sprayers:
- On/off sensor sprayers operate by automatically turning on individual nozzles or sections of nozzles on the spray boom when plants are sensed. Likewise, when no object is sensed, the spray will be turned off (Figure 2a).
- Crop-adapting sprayers are similar in that the sensor is used to turn the sprayer on and off as it passes by plants. However, they go a step further by adjusting application volume, air volume or a combination of those two (Figure 2b).
Sensor controlled sprayers typically have an override where the user can bypass the sensor system and spray as they would with a standard sprayer if, for example, the sensor components of the sprayer are not working.
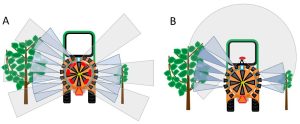
Sensors
Crop sensing systems are the “eyes” of the sprayer and determine crop shape by emitting and receiving signals. There are four basic sensor types used in sensor sprayers: infrared, ultrasonic, plant fluorescence and LiDAR. Each one of these sensors emit their own specific signal aimed at the plants that then bounce off the plants and return to the sensor. Some sensor types require multiple sensors to resolve plant structure characteristics.
Infrared (IR) sensors detect IR signals reflected from the plants and can be used in on/off sensor sprayers. Humidity and temperature do not interfere with IR sensing accuracy. However, low light conditions such as during dawn and dusk can interfere with an IR sensor. IR sensors are unable to accurately resolve plant structure. IR sensors are usually used in canopy spraying to trigger the release of spray from the whole side of a boom when a plant canopy is detected. These systems can also be used for herbicide sprayers. In that case, sensors are aimed at the plant trunks and turn off the sprayer as they pass the trunk, or they can trigger spray directly at the trunk to specifically target suckers.
Ultrasonic sensors emit high-frequency sound waves to measure objects. This process is similar to how bats and dolphins use echolocation to navigate and search for food. When arranged in an array (usually three sensors per side of the sprayer), ultrasonic sensors can detect objects with approximately 4-inch resolution. This allows for calculation of canopy volume with similar accuracy to taking manual measurements. Despite their ability to resolve plant structures, ultrasonic sensors are usually used in on/off sensor sprayers. The initial patents on ultrasonic sensors have expired, so continued off-patent development has improved their quality and capability while reducing costs. Comparatively, ultrasonic sensors are more expensive than IR sensors but less expensive than laser sensors.
Plant fluorescence sensors emit a beam of visible light and detect the light reflected back to the sensor from the plant. These sensors have a spatial resolution of about 4 square inches and can detect a plant area as small as 0.40 square inches. Plant fluorescence sensors can collect plant structure data while in the field that can be stored and used for further planning. These sensors are typically used on “weed-seeing” herbicide sprayers to detect green weed tissue contrasted with the soil surface. They have also been integrated into on/off sensor-controlled canopy sprayers to trigger the spray when a green canopy is sensed.
Laser sensors used to characterize plants are termed LiDAR (light detection and ranging) sensors. These sensors have a laser beam that is directed in an arc around the sensor by a spinning mirror inside the sensor housing. The laser beam is then reflected by any surface it hits, relaying distance and structure information to the sensor. Compared to other sensors, LiDAR most accurately measures crop structure, with resolution to several hundreths of an inch. This gives LiDAR sensors the capability of being used for other tasks while spraying, such as measuring canopy vigor. LiDAR sensors are typically used on crop-adapting sensor sprayers, where only one sensor is needed for each sprayer. These sensors are the most expensive of those listed.
One other sensor is needed for sensor-controlled canopy sprayers. Currently, retrofitted sensor spraying systems are not directly connected to the speedometer on the tractor, so a separate speed sensor is needed to convey the sprayer ground speed to the sensor system. A few examples of speed sensor types used are wheel bolt sensors and radar sensors that use Doppler technology. Maintaining accurate speed detection is critical to ensure spray is released on target.
Sensor Sprayer Efficacy and Efficiency
Insect and disease control with sensor-controlled sprayers has been shown to be similar to that of standard sprayers. Using a LiDAR-based variable rate sprayer has resulted in equivalent control of insect pests, such as codling moth, oriental fruit moth and spotted wing drosophila, to that of an air-blast sprayer. Diseases such as powdery mildew, apple scab, brown rot, anthracnose and mummy berry have also been controlled equal to that of an air-blast sprayer. Ultrasonic sensor-controlled systems have resulted in similar control to standard sprayers on difficult-to-control pests such as apple rust mite and pear psylla and diseases such as apple scab and apple powdery mildew. The amount of spray saved when using sensor sprayers varies, but generally, spray volume savings in the range of 20% to 70% can be seen depending on the sensor system used and the crop. Higher savings typically correspond to more precise sensors such as LiDAR in crops with more variable canopies, while lower-volume savings occur with less precise sensors and less variable crops.
There are a host of other benefits of sensor sprayers beyond spray volume savings. Each spray tank goes further so less time is spent spraying, decreasing the need to refill the sprayer and thus saving on labor. A reduction in the number of sprayer fill-ups required leads to less fuel costs and water savings in addition to a lower amount of wear on the tractor. When spray operations can be completed quicker, it can also make it easier to fit sprays into critical application windows.
Environmental Benefits of Using Sensor Sprayers
Spray drift is greatly reduced with sensor-controlled sprayers. Some studies have shown 23% to 45% of the applied pesticide volume can drift off target using standard air-blast sprayers in orchards. Ultrasonic sensor systems can reduce ground deposition by 70% compared to a standard air-blast sprayer in orchards. Canopy-adapting sprayers can be even more effective at reducing drift in orchards, in one study by 70% to 100% compared to a standard air-blast sprayer depending on the tree growth stage. Lower chemical load on non-target locations also helps decrease the rate of development of pesticide resistance. Other considerations include less pesticide contamination of surface and groundwater and lower chances of exposure on non-target organisms such as beneficial insect populations and livestock.
One Step Further: Autonomous Sensor-Controlled Air-Blast Sprayers
Sensor-controlled sprayers help increase spray application efficiency, but there still needs to be an educated applicator driving the tractor and operating the sprayer. Agricultural labor has become less reliable and more expensive, so some manufacturers are producing autonomous sprayers that can be monitored remotely during a spray process. Global Unmanned Spray Systems (GUSS), Jacto and Hol Spraying Systems, in partnership with AgXeed (Figure 3, see page 6), are three manufacturers that are making fully autonomous self-propelled sprayers for specialty crop production. All three manufacturers are integrating sensors onto the autonomous sprayers to do variable rate spraying. Autonomous sprayers offer lower labor requirements and more efficiency than manned sprayer applications and represent the future of spraying in specialty crops.
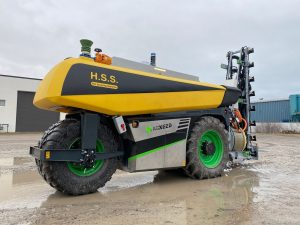
This work was provided in part by the USDA-ARS Integration of Intelligent Spray Technology into IPM Programs in Specialty Crop Production (Project Number 58-5082-2-010).
Resources
Warneke, B. W., Zhu, H., Nackley, L. L., Pscheidt, J. W.(2020) ‘Canopy spray application technology in specialty crops: a slowly evolving landscape’, Pest Management Science, 77(5), pp. 2157–2164. doi: 10.1002/ps.6167.
Nackley, L. L., Warneke, B., Fessler, L., Pscheidt, J. W., Lockwood, D., Wright, W. C., Sun, X., Fulcher, A. (2021) ‘Variable-rate Spray Technology Optimizes Pesticide Application by Adjusting for Seasonal Shifts in Deciduous Perennial Crops’, HortTechnology, 31(4), pp. 479–489. doi: 10.21273/horttech04794-21.
Giles, D. K., Klassen, P., Niederholzer, F., Downey, D. (2011) ‘“Smart” sprayer technology provides environmental and economic benefits in California orchards’, California Agriculture, 65(2), pp. 85–89. doi: 10.3733/ca.v065n02p85.
Chen, L., Wallhead, M., Reding, M., Horst, L., Zhu, H. (2020) ‘Control of Insect Pests and Diseases in an Ohio Fruit Farm with a Laser-guided Intelligent Sprayer’, HortTechnology, 30(2), pp. 168–175. doi: 10.21273/horttech04497-19.