The purpose of this study was to evaluate the effectiveness of the Cotton Clean™ product when applied with various methods and at various rates. The results confirmed what our preliminary research indicated. Generally, the study indicates that Cotton Clean™ shows significant benefit in reducing stickiness on cotton that is at a level of moderate to heavy levels of stickiness. Where stickiness is light or nearly absent, Cotton Clean™ does not have any significant effect on reducing stickiness. From these findings, one may conclude that where stickiness levels are very low to begin with, there may be insufficient food source (deposited insect sugar) for enzymatic sugar reduction through the use of Cotton Clean™. Therefore, the stickiness of cotton with low levels of stickiness do not change with any degree of significance. This is true statistically, as well as economically, as extremely low levels of stickiness generally cause no detectible difference in textile processing or quality of output.
Also, we determined cotton ginned at commercial gins where Cotton Clean™ was applied at time of ginning was significantly less sticky than cotton from the same farm that was ginned at a facility where no Cotton Clean™ was applied at time of ginning.
Introduction
Aphid and whitefly pests are well distributed throughout the San Joaquin Valley and in many other irrigated upland and pima cotton producing regions, particularly where arid conditions exist. It is well documented that several species of these pests can deposit objectionable levels of sugars through their excreta which can make processing seed cotton (in ginning) and cotton lint (in carding and spinning) very difficult and time consuming if sugar deposits reach moderate to high levels. Growers have used many methods and approaches in keeping sticky cotton producing pests to a manageable level, but there are instances where their efforts are ineffective in the avoidance of problematic stickiness levels. When this occurs, gins and spinning mills have severe problems in handling cottons in this condition.
It is believed that if the deposited insect sugar was converted into a substance with little or no viscous properties at ginning or spinning operational temperatures, without harming the cotton fiber onto which it was deposited, then ginning and spinning processes would be improved and lint quality preserved.
In 2016 San Joaquin Valley Quality Cotton Growers Association began work to identify ways to combat the ill effects of sticky cotton beyond control of the insect source itself. A biological agent was introduced on problematic seed cotton that had been plugging up stands at a roller ginning facility. It was sprayed on seed cotton at the module feeder in an aqueous solution. Cotton so treated did not exhibit problems with plug ups at the stands. After that initial trial further study was conducted and it was determined that a more precise formulation could be developed to address Trehalulose and Melizitose even more effectively. In 2017 Cotton Clean™ was developed in conjunction with the manufacturer and their principal dealer. Cotton Clean was provided to 12 different growers for use in applying at harvest and 1 gin used the material applied at the module feeder.
Lint samples were collected from bales treated with Cotton Clean™ and those bales not treated with Cotton Clean™. Those lint samples were tested using Thermodetector, Mini card, and Mesdan ConTest stickiness testing methods. Most test data sets indicated reduced stickiness on samples treated with Cotton Clean™, while a few sets were more inconclusive. Whether or not influential factors not recognized had impacted the results was unclear. Some of those factors are the subject of this project proposal, including rates of application and methods of application. What is known is that ginning personnel report anecdotally that there were no problems with gin stand plugging on cotton treated with Cotton Clean™, whereas, untreated cotton from the same field continued to exhibit plugging problems.
A better understanding of the proper rate of use of Cotton Clean™ and most effective method for application will help growers and ginners make the most of this contamination mitigation tool.
Methods and Materials
Plan of work:
- Identify sources of seed cotton to be included in the study. Growers and ginners in the San Joaquin Valley were contacted to participate as volunteers in the study. In addition to commercial locations, research plots were used as a source of seed cotton.
- Cotton was collected from and ginned at:
- The Shafter Research Station – Farmers Co-Op Gin
- Armstead Ranch – Westhaven Cotton Gin
- Cotton was collected from and ginned at:
- Woolf Farming – Huron Gin
- Errotabere Ranches – West Island Gin
- J. Polder Co. – West Island Gin
- Seed cotton samples (both Upland and Pima) were collected from the fields prior to harvest, identified and segregated so as to preserve identity for both test and control sample sets.
- Varying rates (25 to 90 bales per pound) of Cotton Clean™ were applied through picker moistener systems at time of harvest as well as varying rates applied at time of ginning.
- Lint samples were collected at the gins and transported to secure storage until fiber testing is conducted.
- Lint samples were tested for stickiness using Mesdan Contest instrumentation and recorded.
- Randomly selected lint samples were procured for testing at USDA ARS New Orleans for additional confirmation of results.
- Results were analyzed and reported.
Results
The results from this experiment generally support our hypothesis that Cotton Clean™ reduces the stickiness grades determined by the Mesdan Contest Cotton Quality Testing machine. The overall results from all stickiness levels of cotton in the experiment were slightly in favor of the sample group that had Cotton Clean™ applied. The average stickiness level of the fields without Cotton Clean™ applied during ginning was 102. The average stickiness level of the fields with Cotton Clean™ applied during ginning was 97. A difference of 5 points on the measurement system of the Mesdan Contest machine is insignificant. While it is noted that some field stickiness grade averages were higher with Cotton Clean™ applied than without, those only occurred in samples with low (<100 stickiness grade).
However, when fields with lower levels of stickiness (<100 stickiness grade) were removed from the averaging process, the result is dramatically different. When only those fields with medium to heavy stickiness were considered, Cotton Clean™ applied at ginning reduced measured stickiness significantly, from 147 down to 97, a reduction of 34%.
In order to confirm validity of results measured by the Contest instrument, a random selection of samples from each field was sent to USDA-ARS in New Orleans for blind testing using the standard minicard stickiness test. The minicard test uses a different method of measurement to gauge stickiness levels than the Contest instrument, but has shown relatively good correlation of stickiness between the two measurement technologies. That being said, due to the variability of stickiness among samples within a field the results may also illustrate some degree of variation. The measurements reported by USDA are None, Light, Medium, Heavy, and Very Heavy. In order to make relevant those designations to Contest values, we assigned values we believe to be consistent with similar levels of stickiness as measured by the Contest instrument. None = 10, Light = 75, Medium = 125, Heavy = 200 and Very Heavy = 375. We assigned a numeric value of 10 for None in order to present it graphically, but for all intents and purposes Contest levels of 0 and 10 are effectively indistinguishable.
The results by field for the samples without Cotton Clean™ applied during ginning were 4 fields were None, 10 fields were Light, and 1 field was Heavy. The results by field for the samples with Cotton Clean™ applied during ginning were 1 field was None and 14 fields were Light. None of the samples treated with Cotton Clean™ measured above a Light designation. It should be noted that the minicard designations are subjective evaluations of the technician conducting the test. The difference between Light and None in some instances can be almost indistinguishable. Medium, Heavy, and Very Heavy designations tend to be much more pronounced. So as indicated by the Chart 3, one can see that only where stickiness is more than Light, (in this case Heavy in field 18), can we see significant improvement with Cotton Clean™. This is consistent with the results developed independently with the Contest instrument and so therefore, we conclude the independent results confirm one another.
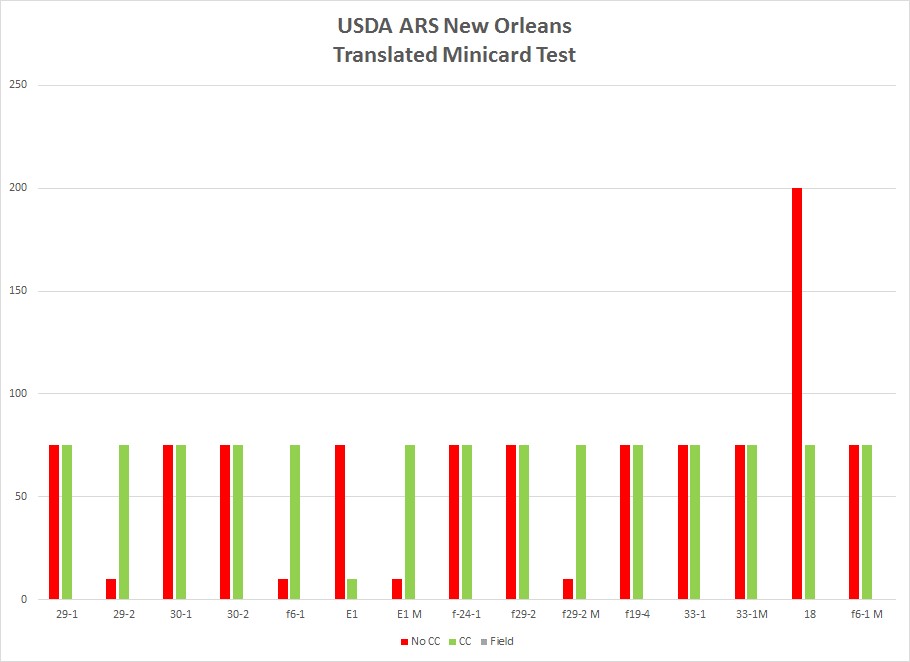
Since only one commercial gin applied Cotton Clean™ uniformly on cotton of a large scale (>10,000 bales) we were only able to evaluate stickiness grades of cotton ginned commercially at one rate (80 bales ginned per pound of Cotton Clean™ applied). At this rate stickiness grades averaged 32 versus an average of 58 for those bales ginned from the same farm but ginned at a ginning facility that did not use Cotton Clean™. Even though all the stickiness levels in this instance were not considered heavily sticky, this large scale test from a farm producing > 10,000 bales indicated that stickiness grades were significantly reduced when Cotton Clean™ was applied at the time of ginning.
Conclusion
Cotton Clean™ shows significant benefit in reducing measured stickiness in instances where stickiness levels in the field are expected to be medium or moderate levels and above. Even when cotton stickiness levels are below moderate, proper application of Cotton Clean™ at manufacturers suggested rates at time of ginning shows significant reduction in measured stickiness.
Acknowledgements
This study could not have been conducted without the assistance and cooperation of many individuals and organizations. We wish to thank all who contributed something to this effort, especially the following: Armstead Ranch, California Cotton Ginners and Growers Association, California State University, Bakersfield, Errotabere Ranches, J. Polder Co., Stone Land Co., USDA ARS New Orleans, Westhaven Cotton Co., and Woolf Farming Co.