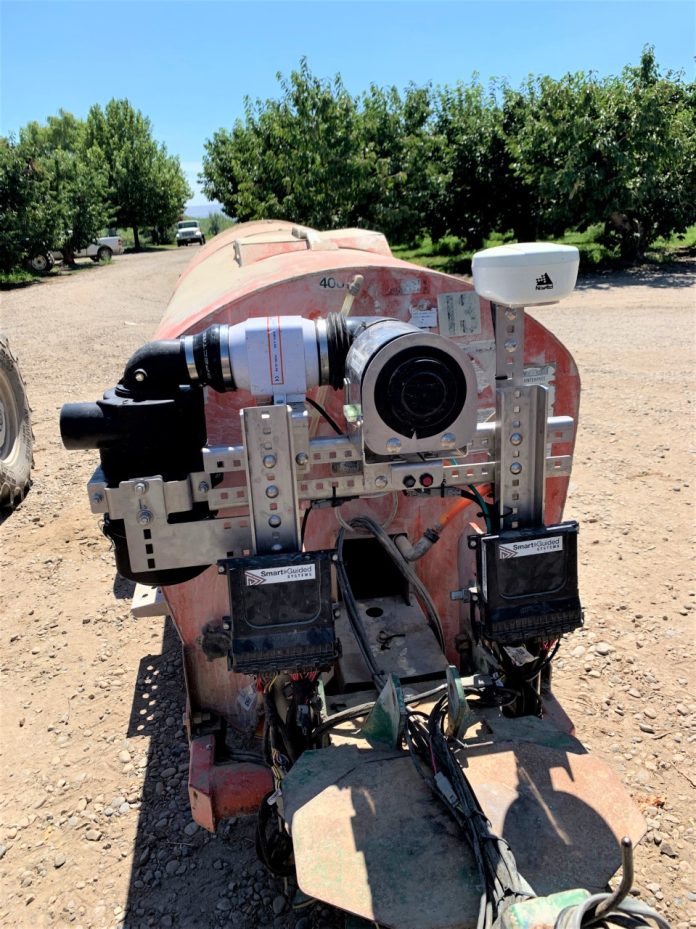
Fruit, nut, ornamental nursery, horticultural and greenhouse industries are among the fastest-growing enterprises in US agriculture. Application of pesticides and other production strategies have ensured their high-quality products meet stringent market requirements. However, low-efficiency, decades-old spray technologies are commonly used to treat these specialty crops and have caused an enormous amount of pesticide waste, additional costs in crop production and concerns around worker safety. The pesticide waste has also caused environmental contamination and ecosystem damage because pesticide sprays indiscriminately kill both pests and beneficial insects. Spray drift and off-target loss will likely remain a major problem as long as pesticides are applied using indiscriminate spray equipment.
Need for Efficient Technologies
Pesticide application is the most complicated operation in crop production because there are many variables affecting spray strategies and practices. In many cases, when decisions must be made to apply chemicals within a very narrow time window in response to escalating pest pressure, a simple “best guess” practice is often under vague labeling of pesticide rates to control pests that may result in excessive application of pesticides.
Given constrained environments for specialty crop production, an ideal spray management program for pests and diseases should include improved delivery systems that are flexible for spraying the amount of chemicals to match tree structures instead of acreage base. Such spray application will also produce minimum spray drift and off-target loss of pesticide on the ground and in the air.
To achieve this goal, a new automated universal intelligent spray control system was developed as a retrofit kit to attach on existing sprayers. With the intelligent control system, the conventional spraying systems can determine the presence, size, shape, and foliage density of target plants such as trees and grape vines, and then automatically apply the amount of pesticides as needed according to plant architectures in real time. With the control system, growers themselves can upgrade their own sprayers to precision sprayers with intelligent functions rather than buying new sprayers, and sprayer manufacturers do not need to change their current sprayer designs. The primary requirement for the upgrade action is to connect a variable-flowrate solenoid valve to each nozzle, and all other components are attached to the sprayer body without changing the sprayer structure.
This new system is the product of a decade of research and development by engineers at USDA-ARS at Wooster, Ohio in collaboration with researchers at The Ohio State University, Oregon State University, University of Tennessee, Clemson University, Texas A&M University, Iowa State University, Washington State University, Penn State University, University of Queensland and USDA-ARS.
Since 2013, the system has been tested as a retrofit on different types of the air-blast sprayers for pest control effectiveness, reliability and repeatability on real farm fields. Comparative field biological tests were also conducted to evaluate insect and disease control for the sprayers with and without the intelligent-decision control capabilities in commercial nurseries, apple orchards, peach orchards, pecan orchards, vineyards and small fruit productions as well as university research farms in Ohio, Oregon, Tennessee, South Carolina, Texas, California and Washington.
These activities were voluntarily held by UCCE in Napa County and University of Queensland in Australia.
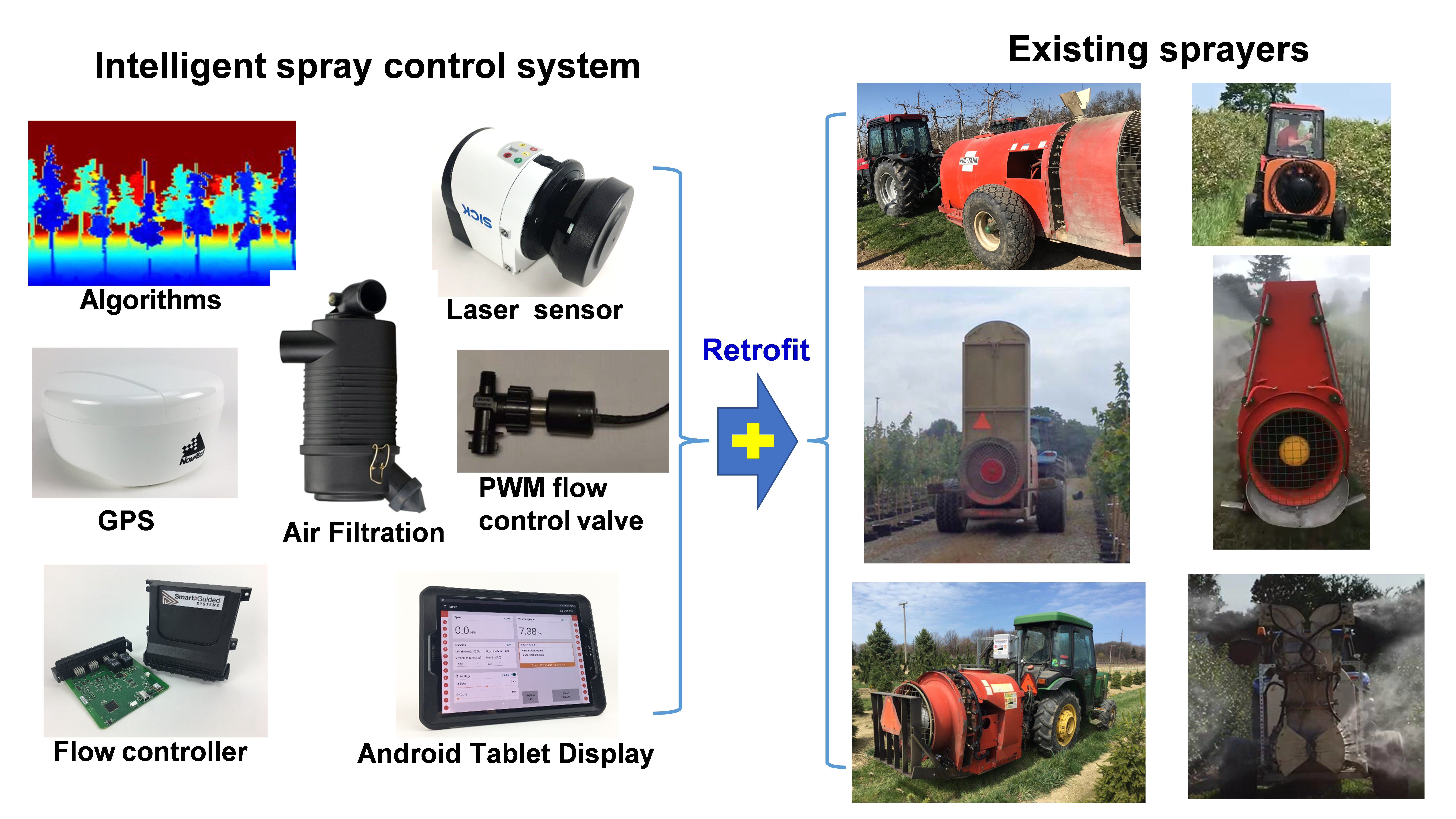
System Features
Spray deposition uniformity insidecanopies, chemical usage and off-target losses were investigated for the plants at different growth stages in ornamental nurseries, apple orchards, peach orchards and vineyards. Multi-year field tests have demonstrated the intelligent spray system is reliable and can reduce pesticide use in a range between 30% and 90%, reduce airborne spray drift between 60% and 90%, and reduce spray loss to the ground between 40% and 80%, resulting in chemical savings in a range of $56 to $812 per acre annually. At the same time, the insect and disease control efficiencies are comparable or even better than standard sprayer practices. Because it uses less spray volume, it can spray more acres with the same amount of tank mixtures, thus reducing tank refilling times and reducing labor and fuel costs.
As a result, Smart Guided Systems, LLC commercialized the intelligent spray system, and a commercial version of the product has been developed with joint efforts between USDA-ARS and Smart Guided Systems, LLC. The new control system (See Figure 1) includes a new laser sensor, an Android Samsung tablet, a GPS navigator, an automatic flow rate controller, air filtration unit, a toggle switch box and a universal mounting kit.
The laser sensor is mounted between the tractor and the sprayer to “see” plants on both sides of the sprayer. It releases 54,000 detection signals per second with a 270-degree and 164-ft radial detection range. The laser signals bounced back from the plant canopies is used to determine the presence of a plant canopy and measure the canopy height, width, foliage density and canopy foliage volume (Figure 2). The GPS navigation device (or the radar speed sensor mounted at the bottom of the sprayer) measures sprayer travel speeds and location of each plant in the field. Based on the plant canopy foliage volume and the sprayer ground speed, the amount of spray for each nozzle is determined and then discharged to different parts of each plant in real time. Each nozzle is connected to a 10 Hz pulse width modulation (PWM) solenoid valve, and the nozzle flow rates are controlled by manipulating the duty cycle of the PWM waveforms with the flow controller. The flow controller consists of microprocessors to generate flow rate commands for each nozzle to discharge variable spray rates. Field data collected and processed with the intelligent spray system are synchronized through the tablet WiFi to the cloud.
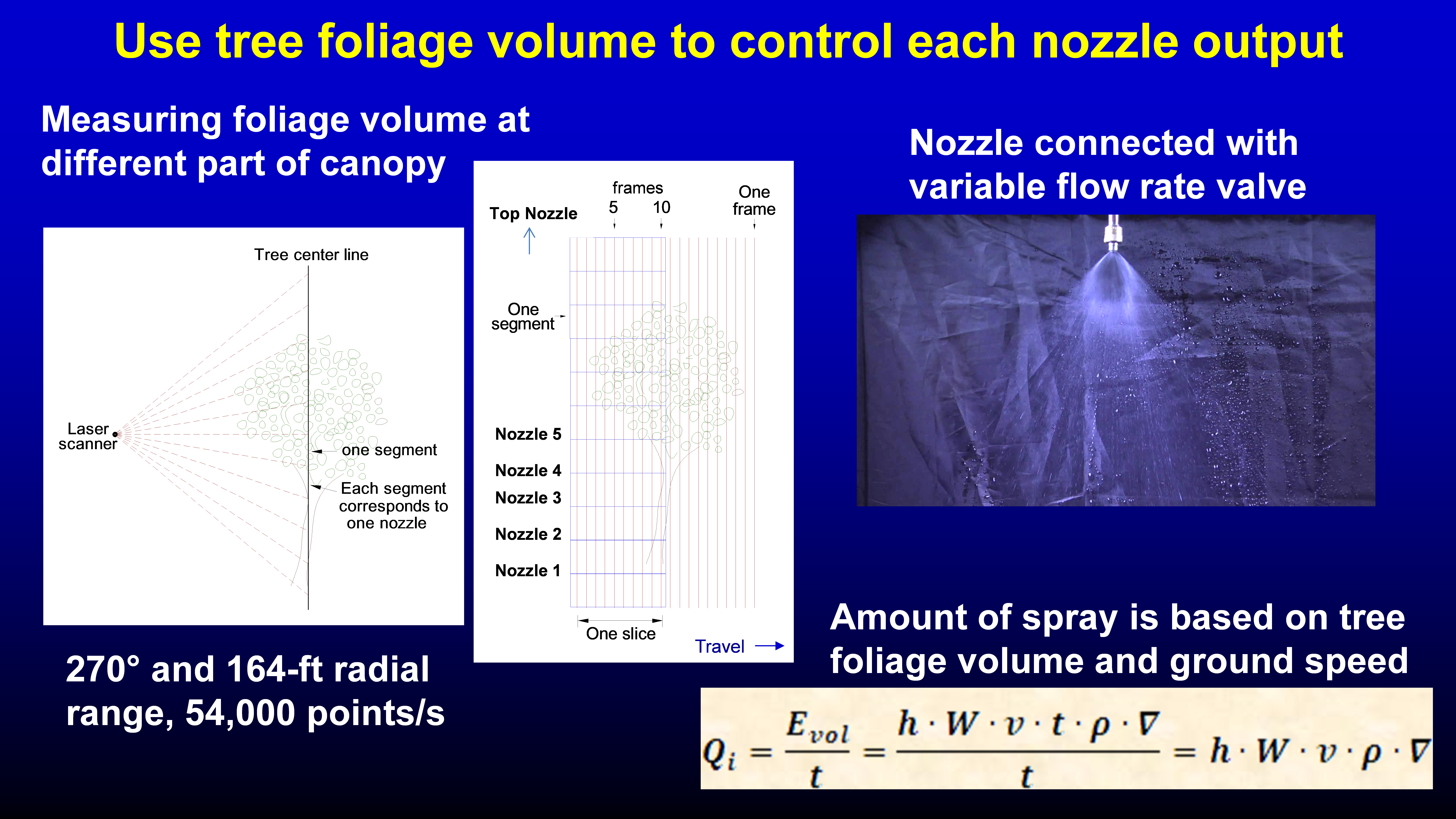
The Android tablet provides the information for operators to communicate with the spray control system. The screen displays the sprayer travel speed, total discharged spray volume, spray width, and active nozzles. The operator can use the touch screen to modify the spray parameters as needed. The tablet allows the operator to activate the sprayer output on one or both sides in manual or automatic mode. All the electronic devices are powered by a 12V DC tractor battery. Another precaution includes the air filtration unit to discharge filtered air to prevent the laser sensor surface from getting dust and droplets. The toggle switches on the switch box are used to turn on/off main power, turn on/off the air filtration unit manually and override the automatic controller to activate nozzles as needed. Because sprayer travel speeds are automatically measured and included in the spray output control, applicators do not need to specify how fast they drive the tractor. However, travel speeds are not suggested to be higher than 5 MPH for orchard spray applications.
Features in the commercial system also include tree counting, tree size, foliage density heat map comparison capability, liquid volume sprayed per plant, maps of sprayed plant locations, ability to turn nozzles on/off independently through the tablet screen, cloud sync feature, web portal for configuration settings and spray coverage report view, system log files, five different languages (English, Spanish, French, German and Italian), and options for choosing metric or imperial units. The commercial products have been used by growers in the US and other countries with crops including citrus, nursery, pecan, blueberry, peach, almond, apple and pear with pesticide usage reductions in the range between 30% to 85% depending on crop types and growth stages. John Deere also established an agreement with Smart Guided Systems to sell the commercial intelligent spray control system for use in high-value crop applications through their dealer network.
The intelligent spray control system advances conventional standard pesticide application systems with the flexibility to spray specific positions on the plants. It reduces human involvement in decisions on how much spray volume is needed because the spray volume applied in the field is automatically controlled by the plant foliage volume instead of the antiquated gallons per acre.
The conventional air-blast spray system has been used from generation to generation for almost 80 years because of its robustness. Growers have accumulated extensive experience on using it to control pests in accommodation with their own crops. After being retrofitted with the intelligent spray control system, the conventional sprayers are able to turn on and off each nozzle and will stop spraying non-target areas such as gaps between trees, on the ground and above trees while their capabilities of spray penetration, spray range and spray deposition quality on plants remain the same. This new generation of spray technology is anticipated to be a primary precision spray technology for future decades to save chemicals for growers and provide a sustainable and environmentally responsible approach to protecting crops.